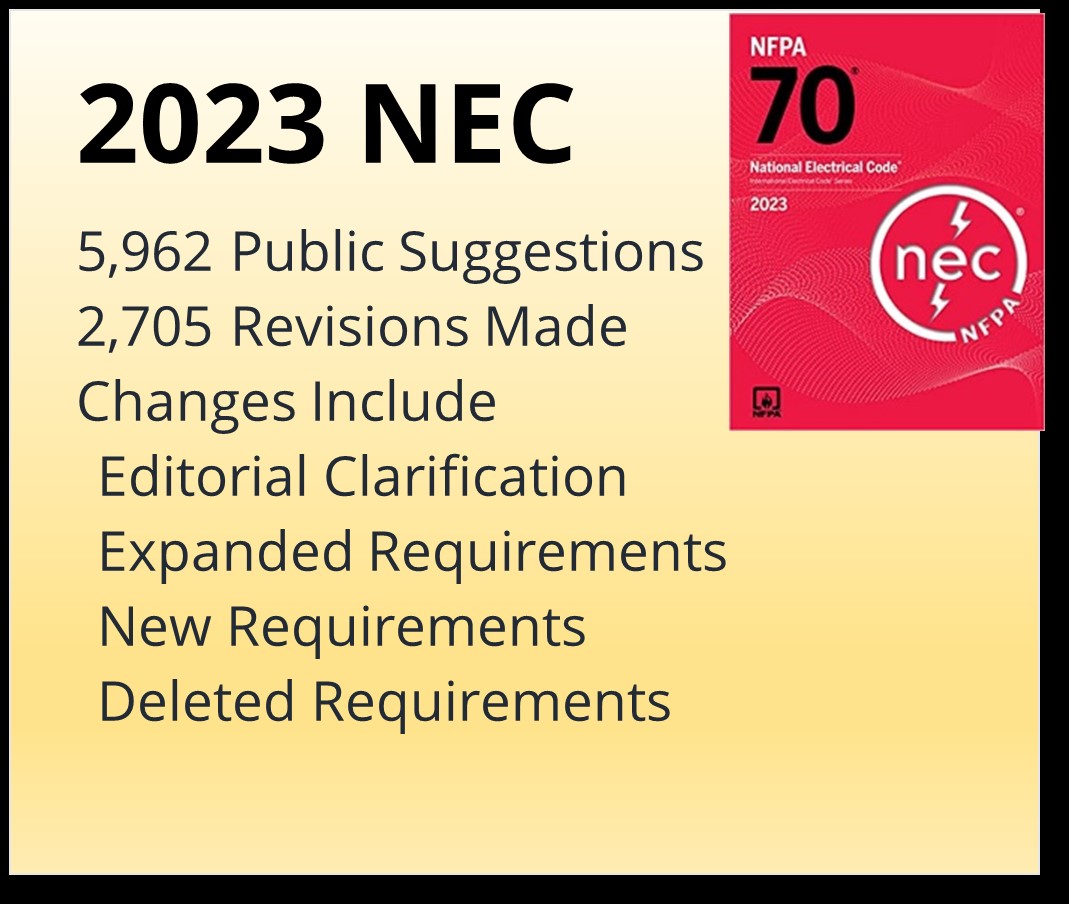
What to Expect
In this course the student will be presented an overview of the most significant changes found in the 2023 NEC. This is part 1 of a series of courses covering the changes and will progress through each chapter and its articles presenting the many important changes. The changes will be underlined for easy recognition and a short synopsis of the reason for the change is presented as well.
Disclaimer
Although every effort has been made to the accuracy of the material presented, by no means shall the student use or substitute this material for official 2023 NEC. Additionally, Ezekiel Enterprises, LLC shall not be liable for any special, incidental, consequential, or exemplary damages resulting, in whole or in part, from the reader’s uses of or reliance upon this material.
Revision – Multiple Articles
Articles 342, 344, 348, 350, 352, 353, 354, 355, 356, 358, 360, and 362
■ What Changed: Multiple Articles were revised by removing the word “Types” from their titles. This coincides with the word “Type” being removed from the new definitions found in Article 100 for conduit and tubings.
■ Its Effect: This change will increase the usability and application
of the NEC by the electrical professional.
Revision – 300.2(A)
Limitations, Voltage
■ What Changed: Section 300.2(A) was modified to add 1500 volts dc in two locations. Rules for medium voltage are being reorganized in the Code in an attempt to increase usability. New articles for installations greater than 1000 volts ac and 1500 volts dc have been added for these items
■ Its Effect: As medium voltage work is increasingly being installed by electrical contractors and not the utility company, focused articles will help with the location of requirements, education, and inspection and will help both installers and inspectors for use.
Revision – 300.4(E)
Ex. No. 1 and 2 Cables, Raceways, or Boxes Installed in or Under Metal-Corrugated Roof Decking
■ What Changed: A new Exception No. 1 and modifications to Exception No. 2 have been added to 300.4(E). These changes recognize poured concrete on top of the metal roof decking as a means of physical protection and addition of “listed steel or malleable iron fittings and boxes” used with rigid metal conduit (RMC) and intermediate metal conduit (IMC). The use of concrete on top of metal roof decking limits screws from penetrating into the raceway system, causing damage to the raceway and wiring. When the metal-corrugated sheet roof decking is covered with a minimum thickness of 50 mm (2 in.) concrete slab, the 38 mm (1 ½ in.) spacing requirements found in the main rule are not necessary
■ Its Effect: The update to 300.4(E) provides clarity to the
installer and the AHJ that abiding by these exceptions will not require the installer to also comply with the main rule requirements of 300.4(E)
Revision – 300.4(G)
Fittings
■ What Changed: New language added in 300.4(G), noting that protective fittings need to be installed “prior to the installation of conductors.”
Installing this fitting after the conductors have been installed allows possible damage to occur to conductors being pulled into the raceway.
■ Its Effect: Even though there are fittings that can be installed after the conductors have been pulled in, this new language will clarify that the intent of the protective fitting is to protect the conductors as they are being put into the raceway and is not intended to be added after the conductors have been installed in the raceway.
Revision – Table 300.5
Minimum Cover Requirements, 0 to 1000 Volts, ac, 1500 Volts dc, Nominal, Burial in Millimeters (Inches)
■ What Changed: Electrical Metallic Tubing (EMT) was added to Column 3 of Table 300.5 to clearly indicate that EMT can be installed in an underground location.
■ Its Effect: This change clarifies for the electrical professional that EMT can be used in underground installations when the UL guide card and Article 358 requirements are followed.
Deletion – 300.5(D)
Protection from Damage
■ What Changed: The words “direct buried” were removed from the text at 300.5(D) by leaving behind “conductors and cables.” As previously written, with the text reading as “direct buried conductors and cables,” this section did not apply to buried raceways containing conductors and only conductors that themselves were directly buried.
■ Its Effect: This revision will provide both the installers and inspectors with clarity as to requirements for underground conductor and cables installations.
Revision – 300.6(A)
Ferrous Metal Equipment
■ What Changed: The informational note referencing field-cut threads was removed, and the reference was turned into positive language.
Adding “anywhere other than at the factory where the product is listed”
provides clarity that threads cut in the field are to be coated with an electrically conductive, corrosion-resistant compound that has been approved for that purpose.
■ Its Effect: This change will allow the AHJ enforcement options by creating positive code language that can be cited instead of pointing the installer to an informational note that is not enforceable and is of an informative nature.
Revision – 300.11(C)
Raceways Used as Means of Support
■ What Changed: Class 3 circuit conductors were added as a conductor permitted to be supported by the raceway containing power supply conductors that supplies the equipment. It was pointed out that there is no basis for allowing Class 2 cables and not also specifying Class 3 cables from being attached to their raceway that supplies the equipment. These cables are typically the same in size and weight.
■ Its Effect: This allows the electrical professional utilization of the same techniques to be used with a Class 3 installation that are currently allowed for Class 2 cables.
Revision – 300.14
Length of Free Conductors at Outlets, Junctions, and Switch Points
■ What Changed: Text at 300.14 was added permitting free conductors to be spliced at outlet, junction, and switch points. The text as it was written left it up to interpretation as to if the free conductor had to be continuous or was permitted to be spliced and extended at the box.
■ Its Effect: This change will aid electrical professionals in interpreting the requirement. It will also be clear that the conductor is permitted to be spliced with a shorter conductor to add length to it and meet the 6 inches required by this section.
Revision – 300.17
Number and Size of Conductors and Cables in Raceway
■ What Changed: Section 300.17 was revised to recognize that cables are
installed in raceways and that requirements are needed so that they are not damaged during and after the installation. The revised Informational Note offers direction to the location of the various wiring methods. The NEC references for “Class 1, Class 2, and Class 3 circuits,” “fire alarm circuits,” and “optical fiber cables and raceways” were changed in the Informational Note. These changes will direct users of the Code to the proper code sections.
■ Its Effect: The revisions to the Informational Note will help direct both installers and inspectors to the appropriate sections for additional information.
New – 300.25
Exit Enclosures (Stair Towers)
■ What Changed: The term “be separated from the building” was removed and the words “have a fire resistance rating” were added to Section 300.25. An exception was also added addressing egress lighting on outside exterior doorways. “Be separated from the building” could mean different things and is not a defined term. “Fire resistance rating” is a defined term in the building code and, therefore, will clarify what the requirement applies to. Outside exterior doorways are part of the means of egress and frequently require egress lighting to extend to the public way. Without the addition of the exception, it was a code violation to provide power to the required exterior egress lighting from the lighting circuit inside the exit enclosure.
■ Its Effect: This revised text will add clarity for the electrical professional regarding this egress lighting requirement. Providing a defined term from the building code makes the requirements easier to understand. The new exception will address a long-standing trade.
New – 300.26
Remote-Control and Signaling Circuits Classification
■ What Changed: A new Section 300.26 was created by for remote-control and signaling circuits. Along with the moving of Class 1 circuitry out of Article 725, this new section directs the Code user to the location of Class 2, and Class 3 circuitry requirements. It also provides necessary clarity on power-limited and non-power-limited installations.
■ Its Effect: This revision will provide much-needed clarity, and approved usability, for remote control and signaling circuit installations for both installers and inspectors.
New – Article 305
General Requirements for Wiring Methods and Materials for
Systems Rated Over 1000 Volts ac, 1500 Volts dc, Nominal
■ What Changed: A new Article 305 was created by for general wiring methods and installations applying to Wiring Methods and Materials for Systems Rated Over 1000 Volts ac, 1500 Volts dc. Before this update, information on medium voltage (MV) installations was scattered throughout multiple sections of the NEC.
■ Its Effect: Consolidating the information for medium voltage (MV) into one article and adding additional information on MV installations will provide the electrical industry, including installers and inspectors, with more guidance in terms of medium voltage (MV) installations.
Deletion – Tables 310.16, 310.17 and 310.20
Ampacities of Conductor Tables
■ What Changed: “XHWN” was deleted from the 90-degree Celsius columns of Tables 310.16, 310.17, and 310.20. The term “XHWN” means an insulation that can be used in dry and wet locations and is of a flame-retardant, moisture-resistant thermoset type. It is listed in Table 310.4(1) as being rated for 75 degrees Celsius.
■ Its Effect: These revisions aid the electrical professional in proper conductor insulation selection and assure these conductors are used properly within the range that it has been rated/tested.
New – 312.10
Screws and Other Fasteners
■ What Changed: A new Section 312.10 was added to address field-installed screws or other fasteners entering a cabinet, cutout box, or meter socket. This additional language protects against damage to conductors resulting from sharp projections from exposed threads of screws that are run through covers. Damage to the conductors has been an issue for some time, creating a shock or fire hazard. This addresses the installation of fasteners that enter into the wiring space.
■ Its Effect: Greater attention will be required by the installer as to the type of fastener they use and how far it protrudes into the wiring space. This will protect conductors from damage from screws and fasteners.
New – 314.5
Screws and Other Fasteners
■ What Changed: A new Section 314.5 was added to address screws and fasteners entering the wiring space of boxes and conduit bodies. This language was added to protect against damage to conductors resulting from sharp projections from exposed threads of screws run through covers or sides of boxes.
■ Its Effect: Greater attention by the electrical professional will be required as to the type and length of the fastener used. Fasteners such as drywall screws will not be acceptable. This will help to protect conductors from damage
New – 314.16(B)(6)
Terminal Block Fill
■ What Changed: New subdivision 314.16(B)(6) was added to address terminal blocks installed in boxes. The word assembly was added so as not to count all the poles of the terminal block for volume allowance towards box fill concerns. Terminal blocks are being used more frequently, and the volume of cubic inches they take up in the boxes needs to be addressed. By adding the word assembly, it can be understood how to calculate box fill for terminal blocks
■ Its Effect: Care must be taken by the electrical professional when choosing the size of box to be used. This will be a better understanding of how to calculate box fill for terminal blocks. When terminal block assemblies are used a larger box could be required based on the box fill calculations. A terminal block could also be added at a later time.
This could possibly create an overfilled box when the terminal block(s) are installed
Revision – 314.24
Dimensions of Boxes
■ What Changed: The existing language at Section 314.24 was adjusted by broadening the reach of this section to address side entries for outlet and device boxes. Outlet and device boxes need appropriate dimensions allowing equipment that is being installed within them to be installed properly without the possibility of damage to conductors that have been installed within the box. This envelope is 1 ¾ in. wide by 2 13/16 inch high, with rounded corners having a radius of 7/16 inch, and several devices take advantage of this profile.
■ Its Effect: The electrical professional will need to become aware of these requirements to assure that boxes of the proper size are installed in the field. There will need to be communication between the authority having jurisdiction (AHJ) and the installers as to what devices are intended to be installed in boxes to assure the box is of the appropriate size.
New – 315.1
Scope
■ What Changed: Clarifications made as to the voltages covered by Article 315, which is entitled Medium Voltage Conductors, Cable, Cable Joints, and Cable Terminations. Article 311 has been deleted with those requirements relocated to Article 315. New requirements for cable joints and terminations were also added to this article. Specification of the voltage requirements was needed to improve the usability of the Code. This article includes voltages from 2001 volts to 35,000 volts. This article does not include voltages from 2001 volts to 2500 volts dc, nominal or voltages above 2500 for dc circuits.
■ Its Effect: This information will help the electrical professional assure the conductors are installed properly and within the range they are rated/tested. This revision will also add clarity for the user at 315.16 on how to identify Type MV, medium voltage cable.
Revision – 320.23(A)
Cables Run Across the Top of Framing Members. (In Accessible Attics)
■ What Changed: The term “Framing Members” replaced the word “Joists” in Section 320.23(A) when considering the installations of armored cable: Type AC. Most attic locations do not contain floor joists; they have ceiling joists. This change is made to eliminate confusion for ceiling or floor locations where cables are installed by using the phrase “framing members.”
■ Its Effect: This change adds clarity for the installer and AHJ when making interpretations of code language reflecting the location designated as “In Accessible Attics.”
Revision – 322.56(B)
Taps
■ What Changed: Changes made to flat cable assembly requirements by removing the term “color-coded” and replacing it with “marked” in Section 322.56(B). The term “color-coded” was changed to “marked” to correlate with the terminology found at 322.120, which is entitled “Marking.” This change does not change the meanings of the requirements found at this location.
■ How this will affect the electrical industry:
■ Its Effect: This change will provide clarity and unison with other code sections. It allows “marking” for conductor taps for flat cable assemblies (Type FC) to be installed per requirements found at 322.56(B).
Revision – 330.112(A)
1000 Volts or Less. (MC Cable)
■ What Changed: Few editorial changes added in Section 330.112(A) to correlate with the addition of 16 AWG copper conductors for general use wiring methods used with metal-clad cable (Type MC). The recognition of 16 AWG copper conductors for use as ungrounded, grounded, and equipment grounding conductors in 330.104 was necessary for the useability of the Code. These shall be of a type that is listed in Table 310.4(1) for conductor applications and installations rated for 600 volts.
■ Its Effect: This revision will clarify and allow the use of 16 AWG as control and signal circuits for ungrounded, grounded, and equipment grounding conductors.
Revision – Article 337
Industrial Mobile Cable: Type IM
■ What Changed: All references to the former Type P cable to Type IM in Article 337 was changed. Installation requirements can be found in this article for topics such as bending radius, ampacity, listing, and uses permitted or not permitted. This article should not dwell on marine-type installations, as most would not be found in the scope of the NEC. Type P cables are used for offshore drilling rigs and not under the purview of the NEC.
■ Its Effect: This revision will clarify for the electrical professional the application of this type of cable and the severe environments that it is capable of functioning in.
Revision – 342.20(B)
Maximum
■ What Changed: Section 342.20(B), was revised for intermediate metal conduit (IMC) by specifying that a 6-inch trade size is the largest that can be installed.
■ Its Effect: This change would allow for the use of Trade Size 5 and 6 IMC. It should be noted that UL standard 1242 does not currently include IMC trade sizes 5 and 6. It will be of concern for AHJs, installers, and designers that they are able to comply with 342.6 regarding listing requirements.
Revision – 344.28
Reaming and Threading (Rigid Metal Conduit)
■ What Changed: Clarification added for adherence to the manufacturer’s requirements for reaming and threading of PVC-coated rigid metal conduit (RMC) in Section 344.28. This change was due to installers accidentally damaging PVC rigid metal conduit when they were reaming and adding threads to the conduit. A new informational note was added to assist installers with this procedure.
■ Its Effect: This guidance will help assure this product (when field modified by cutting, reaming, and threading) is not damaged and can function properly in the environment it is being used. The electrical professional will need to utilize the correct tools and follow the manufacturer’s guidelines when installing this product.
New – 352.44(B)
Expansion Fittings (Earth Movement)
■ What Changed: Requirements added for an expansion fitting to be installed for underground runs of direct buried PVC conduit that emerge from the ground. Different soil conditions and weather conditions exist, and this change attempts to eliminate damage to PVC conduit and electrical equipment and enclosures from occurring.
■ Its Effect: The electrical professional will need to provide expansion fittings for PVC conduit installations emerging from the ground. When necessary, these should be provided above grade to compensate for earth settling or movement.
Revision – 353.48
Joints
■ What Changed: Section 353.48 was revised by to specify that the joining methods of High Density Polyethylene Conduit (HDPE) are to be made by a method identified by the manufacturer. Heat fusion or butt fusion joints are not to be permitted. Heat or butt fusion joining methods result in an internal lip or bead formed on the conduit ID, which may “burn” or damage the cabling when it is subsequently pulled over the lip. Additionally, the lip will reduce the potential wire pull surface area and conduit fill calculations.
■ Its Effect: This change will affect the electrical inspector and installer by not requiring an “Approved method” for joining HDPE conduit. Joints shall be made by a method identified by the manufacturer, while heat fusion or butt fusion joints are not permitted.
Revision – 358.20(B)
Maximum
■ What Changed: The maximum size of electrical metallic conduit (EMT) was increased to metric designator 155 (trade size 6) in Section 358.20(B). There is a need for 5- and 6-inch EMT that is not being addressed in the current Code. The 5- and 6-inch EMT is similar to materials used to create 5- and 6-inch rigid metal conduit (RMC), which have a proven result. The outer diameter of 5- and 6-inch EMT will be the same as 5- and 6-inch RMC but will have a thinner wall.
■ Its Effect: This change would allow for the use of 5- and 6-inch EMT.
New – Article 369
Insulated Bus Pipe (IBP)/Tubular Covered Conductors (TCC), Systems
■ What Changed: A new Article 369 was added to cover the use, installation, and construction specifications for insulated bus pipe (IBP) systems.
Insulated bus pipe systems (IBP) are not new to the electrical industry. IBP systems are currently in use or being installed by both U.S. and Canadian-based utilities. These systems can be used for both indoor & outdoor locations. The system incorporates cable systems, bus bars, metal-enclosed bus, resin-impregnated bushings, and tap boxes. Insulated bus pipe (IBP), also known as Tubular Covered Conductor (TCC), has been used for many years in shipboard and utility applications in Europe and utility applications in the United States. These systems are lighter, consume less volume, and take less time to install than a traditional system. It has been proven as a practical alternative to using medium voltage cables, bare busbars, or bare conductors. They could provide a level of safety equivalent or better than those wiring methods that are already allowed in locations accessible to qualified persons only when listing becomes available.
■ Its Effect: It is important for inspectors, installers, and designers to note that (IBP) and IBP systems shall be listed per NEC 369.9 and must be installed by qualified persons, with all documentation made available to the authority having jurisdiction.
New – Article 371
Flexible Bus Systems
■ What Changed: Article 371 was created to address the new product (Flexible Bus Systems), which provides many of the benefits of both bus duct and cable. It can easily be customized during installation in the field to account for field conditions. It is not rigid and does not have the bending radius limitations that cable has; therefore, it allows installation where there are space limitations or structural interference. Its flexibility reduces installation time by making it easier to make connections in the field without the need for special tools. It is light in weight compared to an equivalent bus duct or conductors in a conduit. It may reduce the installation time and cost associated with the electrical installation.
■ Its Effect: It is of special interest to inspectors, installers, and designers that flexible bus systems be listed per NEC 371.6. Currently, there is not a specific standard available for listing this product.
Deletion – 398.15(C)
Exposed to Physical Damage
■ What Changed: High-density polyethylene conduit (HDPE) was removed as a permitted means to provide physical protection for open wiring on insulators in Section 398.15(C). It was discovered 353.12(1), Uses Not Permitted, prohibits its use for exposed installations. This conduit is also not permitted within a building per 353.12(2
■ Its Effect: The installer and the inspector will need to conduct an assessment to make sure that the marking will stay adhered to the electrical equipment. These requirements will ensure the safety of the electrical professional as well as keep important hazard labels and signs where they need to be installed.
New – 404.1
Wall-Mounted Control Devices
■ What Changed: A new informational note was added to Section 404.1 addressing wall-mounted control devices. Battery-powered wireless lighting
wall control devices are a new technology, and guidance was needed as to how they should be addressed.
■ Its Effect: With the addition of the informational note, the electrical professional will have a better understanding that these wireless switch devices are not under the purview of the Code.
New – 404.14(D)
Snap Switch Terminations
■ What Changed: A new 404.14(D), Snap Switches with Push-In Terminals, was inserted in between the pre-existing subdivisions. The change to this section is to highlight this limitation for switches that may have push-in terminals provided. The introduction of 14 AWG copper-clad aluminum into the NEC for branch circuit wiring needs this limitation to ensure push-in terminals on wiring devices are installed according to their listing.
■ Its Effect: The clarification for 14 AWG solid copper conductors to be used with push-in terminals of snap switches ensures that the authority having jurisdiction (AHJ) and other electrical professionals will be provided with the intended requirements for use.
New – 404.16
Reconditioned Equipment
■ What Changed: The change: New Section 404.16 was added to address reconditioned equipment. This change addresses control devices that can and cannot be reconditioned after being damaged. Damage might occur to control devices after being subjected to water, fire, or products of combustion. The reliability or function may be compromised if reconditioning of the items is attempted.
■ Its Effect: In cases where the control device has been subjected to damage from water, fire, or products of combustion, they can not be cleaned and put back into service. An inspector will have to be keen on what to look for to determine if the device was replaced or not.
New – 404.30
Switch Enclosures with Doors
■ What Changed: Text added to clarify the requirement for doors with switch mechanisms. Switches of this type may allow access to live parts with the door open that unqualified persons may come into contact. Access
to the interior of a switch in the closed position will require the use of a tool. An approved design providing equivalent protections is also allowed.
■ Its Effect: The electrical professional will need to be aware of these changes and ensure the proper switch enclosure has a door with these provisions. This needs to be installed and verified before the installation is put into service.
Relocation – 406.2
Reconditioned Equipment
■ What Changed: Limitations for reconditioned equipment from 406.3(A) and 406.7 were relocated into new Section 406.2 for consistency and better usability of the Code. Relocating reconditioning requirements into one section within Article 406 for receptacles, attachment plugs, cord connectors, and flanged surface devices provides one location for the user of the Code to find these requirements.
■ Its Effect: The xxx.02 sections of NEC articles are becoming the placeholder for reconditioned equipment requirements. Combining all reconditioned requirements and limitations in 406.2 will improve the useability for the electrical professional.
New – 406.3(D)
Receptacle Terminations
■ What Changed: The new text added in 406.3(D) is intended to emphasize the limitations for receptacles installed on 15-ampere branch circuits. Only 14 AWG copper conductors used with “push-in” type terminals for receptacles are permitted. The old text at 406.3(D) has been moved to subdivision (E).
■ Its Effect: The new text will ensure inspectors and the installers will better understand the limitations of the terminations on receptacles. The additional text will reemphasize the type of conductors allowed based on the specific markings on the receptacle terminals. There has also been confusion within the electrical industry on the proper use of push-in type terminals and the type and size of conductors allowed to be terminated into these push-in type terminals. This new text will clear the confusion and alleviate future misapplication of the size and type of conductors allowed in push-in type terminals.
Revision – 406.4(D)(3)
Ground-Fault Circuit-Interrupter Protection
■ What Changed: Ground-fault circuit interrupter (GFCI) receptacles are now required to be listed per 406.4(D)(3). By adding this requirement, the public will be assured that all GFCI’s are listed and manufactured according to the minimum standards set forth in UL 943, Ground-Fault Circuit Interrupters.
Also revised the term “outlet,” was removed which improves and clarifies the intent of the current Code
■ Its Effect: Requiring the listing specifically within Article 406 will add clarity for the electrical professional and remove any uncertainty about whether these GFCI devices are or are not required to be listed. Listing of these and other electrical equipment assists in providing safe electrical products and assures all electrical devices are manufactured to the same standard and the same safety technologies are being provided for
GFCI receptacles.
New – 406.4(D)(8)
Ground-Fault Protection of Equipment (GFPE)
■ What Changed: New requirement added to require ground-fault protection of equipment (GFPE) to be provided for replacement receptacles that now require GFPE protection by the current Code. This requirement is very similar to section 406.4(D)(3) of this section, which requires ground fault
circuit-interrupter (GFCI) protection to be provided if a receptacle is replaced where the NEC presently requires GFCI protection. A
■ Its Effect: This new requirement will improve the safety of electrical systems that have been installed previously and will enhance the safety for the people who use electrical systems where the ground-fault protection of equipment is required by newer versions of the Code.
Revision – 406.6(D)
Receptacle Faceplate (Cover Plates) with Integral Night Light
and/or USB Charger
■ What Changed: Revised language to 406.6(D), limiting the faceplate’s load
to one watt or less and specifically requires the screws on the receptacles to be made only of brass or copper alloy.
■ Its Effect: There has been uncertainty if these devices were safely connected to receptacles by friction contact with the screw terminals. This change will add clarity for the electrical professionals that they are safe to install. This change will allow these faceplates to be used as they have been in the past but will limit the wattage allowed to be carried thru the connection points between the receptacle and the faceplates. The new language also requires these faceplates to be utilized with receptacles equipped with brass or copper alloy only.
Revision – 406.9(C)
Bathtub and Shower Space
■ What Changed: Clarification of receptacle restrictions in and around bathtubs and showers in Section 406.9(C). A new Exception #4 was added to allow single receptacles within 36″ of the tub or shower with limitations.
This change was accepted because the area below the bathtub rim was not
included in the language added in the 2020 NEC. The areas outside of and below the rim of a bathtub are just as important as the area above the rim extending out three feet. A new Exception #4 was added to accommodate the toilets with electronic seats and other functions, which require 120-volt receptacles to be installed within the 36″ zone or personal hygiene devices for people with physical limitations. This receptacle is required to be a single receptacle and not be located in the space between the bathtub or shower and the toilet or bidet.
■ Its Effect: These changes help clarify the receptacle requirements for the electrical professionals in areas containing a bathtub or shower space. They will enhance the safety within these areas.
Revision – 406.12
Tamper-Resistant Receptacles
■ What Changed: Revision includes some editorial changes to allow for an easier understanding of where tamper-resistant receptacles are required. Additional areas and occupancies were also added where tamper-resistant receptacles will now be required.
■ Its Effect: The editorial changes made within the subdivisions of 406.12 will make these requirements and where the tamper-resistant receptacles are required easier to understand for the electrical professional. The expansion of the areas requiring tamper-resistant receptacles will provide an additional level of safety for the occupant in these occupancies.
Revision – 408.4
Descriptions Required
■ What Changed: This revision placed requirements for circuit directories and descriptions in Section 408.4 into a list format for clarity.
■ Why it happened: There was confusion with the previous text as written in paragraph form. Generalized labeling was removed in a previous cycle, but there was still confusion left when looking at it in the field as to what was being written. The new list format layout for these requirements is for the end user’s benefit.
■ Its Effect: This change will clarify labeling and description for panelboards and panels for the electrical professional.
Revision – 408.9
Replacement Panelboards
■ What Changed: The replacement requirements for panelboards in Section 408.9. were revised for clarification. There are now two list items for the replacement of existing panelboards in an enclosure or cabinet.
■ Its Effect: This offers a degree of clarity to the electrical professional regarding the replacement of a panelboard within an existing cabinet. There has been confusion regarding the replacement of a panelboard. Can one manufacturer’s panel board be installed in another manufacturer’s cabinet? What is the panelboard is no longer available from a specific manufacturer? This will alleviate the confusion that exists between the AHJ and the installer when these instances present themselves in the field.
Revision – 408.38
Enclosure
■ What Changed: Text revised where a panelboard installed in a cabinet, cutout box, or identified enclosure has an available fault current greater than 10,000 amperes, the panelboard and enclosure combination shall be evaluated for the application.
■ Its Effect: This offers guidance and a degree of clarity to the electrical professional when panelboards with a deadfront are installed in cabinets, cutout boxes, or other identified enclosures. An exception for installations that are not associated with dead fronts is allowed to be accessible only to a qualified person.
Revision – 408.43
Panelboard Orientation
■ What Changed: Section revised adding that panelboards cannot be installed in the face-down position. The face-down position criteria were added due to working space concerns. Even with acceptable working space, it would be very difficult for a qualified worker to safely work in this position due to the installer lying, kneeling, or standing on a floor surface looking up.
■ Its Effect: This revision in 408.43 clarifies how panelboards can be installed. It now includes language for the electrical professional that these items cannot be installed in the face-up or face-down position.
Reorganization – 409.60
Bonding
■ What Changed: Section 409.60 for industrial control panels was restructured, creating (A) Grounding and (B) Bonding to clarify where grounding and bonding would occur and have the revised language comply with the section title. Further clarification was added to indicate applicable sections for sizing these grounding and bonding conductors.
■ Its Effect: The reorganization of 409.60 will clarify to the Code user that grounding and bonding are required for these industrial control panels and provide the applicable code sections based on which direction or situation is present.
New – 409.70
Surge Protection
■ What Changed: New Section 409.70 has been added requiring surge protection for industrial control panels. In previous editions of the NEC, surge protection wasn’t required in industrial control panels.
■ Its Effect: The added requirement at Section 409.70 provides a level of equipment and personnel safety for the electrical professional when working on industrial control panels. Additionally, a level of equipment protection is also inadvertently provided.
Revision – 410.2
Reconditioned Equipment
■ What Changed: Revision added specifying ballasts, LED drivers, and lamps should be added into updated Section 410.2 for items not allowed to be reconditioned. The 2023 change will add lighting ballasts, LED drivers, and lamps to this existing list of items.
■ Its Effect: The addition of these other items will assist the electrical professional in maintaining the safety of the public. It also adds clarity and usability to the Code.
Revision – 410.10(F)
Luminaires Installed in or Under Roof Decking
■ What Changed: This requirement has been revised to require luminaires to be located a minimum of 38 mm (1 ½ in.) from any type of roof. An exception was also added for concrete of 50 mm (2 in.) covering metal-corrugated sheet roof decking that the 38 mm (1 ½ in.) spacing is not required.
■ Its Effect: The electrical professional will need to understand that this change expands the requirement for luminaires for all roof systems to be a minimum of 1 ½ inch from the lowest part of the roof system. This will assure other trades, such as roofers, will be less likely to damage luminaires installed near the underside of roofs. This will now apply to all roofs in all occupancies; therefore, dwellings will now be more likely to be affected by this requirement due to the fact this applies to all roofs. Previous editions of the NEC only applied to metal corrugated roof systems, which are typically installed on commercial or industrial buildings.
Relocation – 410.71
Disconnecting Means for Fluorescent or LED Luminaires the Utilize Double-Ended Lamps
■ What Changed: The requirement for disconnects for luminaires was relocated to 410.71 because LED drivers were added to this section. Lighting systems have evolved, and fluorescent lamps are being discontinued and replaced with LED lamps. Man of the existing fluorescent luminaires are being upgraded to incorporate LED lamps to meet energy conservation requirements. The additional requirement for LED luminaires was added to address a hazard that would exist with either style of luminaire.
■ Its Effect: The electrical professional will need to know that the information previously located in 410.130(G) is now located at 410.71. This change will better align the wiring requirement within Article 410. It will also make the installation safer for the installer and the maintenance personnel who may be involved with repairing and maintaining the luminaire.
New – Article 410, Part XVII
Special Provisions for Germicidal Irradiation Luminaires
■ What Changed: A new Part XVII was added to Article 410 to address the increasing use of germicidal luminaires for disinfecting purposes. These products are increasingly being used due to the COVID 19 pandemic and other concerns.
■ Its Effect: Bringing these requirements into the NEC allows the installer and the AHJ to understand the limitations and installation requirements for the specialized luminaires.
Revision – 410.184
Ground-Fault Circuit-Interrupter (GFCI) Protection and Special
Purpose Ground-Fault Circuit-Interrupter (SPGFCI) Protection
■ What Changed: Section 410.184 was revised to clarify when GFCI protection is required for horticultural lighting, with an exception added to require the use of a special purpose ground fault circuit interrupter (SPGFCI) on circuits exceeding 150 volts to ground. An Informational Note was also added to point readers to UL 943C, Outline of Investigation for Special Purpose Ground-Fault Circuit-Interrupters, for further information on SPGFCI devices.
■ Its Effect: The revisions will provide relief to the electrical professionals from having to provide GFCI or SPGFCI protection for 277-volt, cord-connected, horticultural lighting that is hard-wired. Electrical inspectors will have clear and enforceable Code language and will no longer have to resort to using 90.4 to approve an installation.
Deletion – Article 422
Appliances
■ What Changed: Sections 422.3, 422.4, 422.15, 422.23, 422.46. 422.50 for appliances were identified as redundant or unnecessary and deleted from the 2023 edition of the NEC. Many of the removed sections are covered in the listings.
■ Its Effect: Deletion of this material does not reduce safety as the material is covered in product standards or in other general requirements in the NEC. This allows installers and AHJs to simply confirm listing and utilize nameplate ratings to verify installation requirements.
Revision – 422.16(B)(2)
Built-in Dishwashers and Trash Compactors
■ What Changed: Provisions added at Section 422.16(B)(2) for supply cords to trash compactors and dishwashers to pass through an item such as a wood cabinet to be provided with protections that incorporate smoothed edges. While grommets and bushings are practical solutions in metal cabinet separations, those fittings were not practical with wood cabinets.
■ Its Effect: While previous text allowed other approved means as an acceptable means to protect cords, this revision eliminates the need for a judgment call when an obvious solution exists. This should clarify issues between the installer and the inspector when they arise in the field.
Revision – 422.18
Ceiling-Suspended (Paddle) Fans
■ What Changed: Text covering ceiling-suspended (paddle) fans have been subdivided and includes a new first-level subdivision (B) that prohibits metal parts of ceiling fans from areas over tub and shower spaces. That prohibited “zone” correlates with the prohibited zone described in 410.10(D) for luminaires. This prohibited zone for luminaires recognized an elevated risk where an individual could touch the luminaire while standing in the water. This change correlates the ceiling fan requirement with luminaires since the risk is similar.
■ Its Effect: Many electrical professionals were already likely applying the requirement in 410.10(D) to ceiling fans. This change improves usability by including text to provide equivalent safety to installations with similar risks.
Deletion – 424.10
General
■ What Changed: Section 424.10, Special Permission, was deleted and 424.9, General, was relocated to 424.10 at the beginning of Article 424 Part II.
■ Its Effect: While the provision for use of special permission was removed from Article 424, AHJs can utilize 90.4 where an equivalent installation is provided and the option for special permission is needed for approval. This will add clarity and usability to the Code.
New – 424.48
Installation of Cables in Walls
■ What Changed: The new section at 424.28 was created and will allow heating cables to be installed in walls with specific protection and limitations. The provision includes a January 1, 2026, effective date. While concerns exist for heating cable installed in walls, the need for that installation with proper protection was evident. Installations were already being considered in Canada to permit these types of installations with adequate protection. Understanding that installation codes, product standards, and certification would all need correlation and some effort to determine the heating products would be operating with available protection resulted in the future effective date.
■ Its Effect: This change allows equipment manufacturers, standards developers, and certification agencies an opportunity to develop products and address interoperability issues before the effective date.
New – 424.93(C)
Installation of Heating Panels in Walls
■ What Changed: This new first-level subdivision created will allow heating panels and heating panel sets to be installed in walls with specific protection and limitations. The provision includes a January 1, 2026, effective date.
■ Why it happened: While concerns exist for heating panels and heating panel sets installed in walls, the need for that installation with proper protection was evident. Understanding that installation codes, product standards, and certification would all need correlation and some effort to determine the heating products would be operated with available protection resulted in the future effective date. This revision correlates with requirements in 424.48 for heating cables.
■ Its Effect: This change allows equipment manufacturers, standards developers, and certification agencies an opportunity to develop products and address interoperability issues before the effective date.
Deletion – 425.10
General
■ What Changed: Section 425.10 was deleted for special permission requirements and 425.8 General was relocated to 425.10 as the beginning of Article 425 Part II. The 2020 NEC included a provision to permit the installation of industrial process heating equipment by methods other than those included in Article 425 with special permission. This provision was determined to be redundant as 90.4(C) permits the use of special permission.
■ Its Effect: While the provision for use of special permission was removed from Article 425, AHJs can utilize 90.4 where an equivalent installation is provided, and the option for special permission is needed for approval.
Deletion – 426.14
Special Permission
■ What Changed: Section 426.14 pertaining to special permission for fixed outdoor electric deicing and snow-melting equipment was deleted. This provision was determined to be redundant as 90.4(C) permits the use of special permission.
■ Its Effect: While the provision for the use of special permission was removed from Article 426, AHJs can utilize 90.4 where an equivalent installation is provided, and the option for special permission is needed for approval.
Revision – 426.28
Ground-Fault Protection
■ What Changed: Manufacturers of fixed outdoor electric deicing and snow-melting equipment have an option to require ground-fault protection with reduced current and time threshold values providing a higher degree of protection than previously required. Therefore, Section 426.28 was revised, allowing the manufacturer to specify the ground fault trip level.
■ Its Effect: While NEC 110.3(B) is not new, this change is a clear application where utilization equipment manufacturers have included “additional” protection for the utilization equipment. Designers, installers, and AHJs must review installation instructions prior to installation to assure compliance.
Deletion – 427.35
Scope
■ What Changed: Section 427.35, which covered the installation of line frequency induction heating equipment and accessories for pipelines and vessels, was deleted. This section was determined to be redundant as 427.1 already covers the scope of the article
■ Its Effect: This specialized heating equipment will continue to be covered by this article. The removal of the scope requirements at 427.35 will increase usability and reduce confusion for the electrical professional.
Revision – 430.1
Scope
■ What Changed: The previous figure at Section 430.1 has been deleted, and an expanded figure has been added to include all relevant parts of the motor circuit and what parts of Article 430 apply. The previous figure in 430.1 has been in the NEC for several decades. The revised figure provides a pictogram of the various elements of a motor circuit and includes the applicable part where information can be found within Article 430.
■ Its Effect: This change provides a more comprehensive detail for motors and their control devices. The electrical professional will be provided with additional clarity and application to the various requirements that apply to this equipment.
New – 430.2
Reconditioned Motors
■ What Changed: New guidance added for reconditioning of motors in Section 430.2, including a new informational note that references ANSI/EASA AR100-2020, Recommended Practice for the Repair of Rotating Electrical Apparatus. The new informational note references ANSI/EASA AR100-2020, Recommended Practice for the Repair of Rotating Electrical Apparatus. This information is helpful if the reconditioning facility is no longer in business. This reference contains valuable information about the rewinding and repair of electric motors.
■ Its Effect: Most electrical professionals are aware that motors are being reconditioned and safely placed back into service. There is now language in the NEC that provides guidance and acceptance for this practice.
Revision – 440.8
Single Machine and Location
■ What Changed: New language has been added to Section 440.8, indicating that mini-split units are not to be installed in a tub or shower zone.
Mini-split heating and cooling systems are being installed in bathtub and shower spaces due to a lack of wall space. This is increasingly occurring in older homes with smaller bathrooms where the shower was on the outside wall, making it a prime place to install these systems. This installation provides a clear danger to the occupants, and the new language revises Section 440.8 to prohibit the installation of these units in the zone around bathtub and shower spaces. The dimensions of the zone stated with this change are consistent with code requirements for other electrical equipment or devices.
■ Its Effect: This added language makes it clear to installers and inspectors that mini-split systems are not allowed in a tub and shower zone.
Revision – 440.11
General
■ What Changed: Additional language added at Section 440.11 that requires disconnects with covers that expose live parts to be locked for protection.
Language was added requiring air-conditioning and refrigerating equipment
disconnects that have hinged covers, and when open, have exposed live parts, be locked to prevent children and unqualified people from accidental contact. As “zip-ties” would require the use of a tool to remove the cover; it is allowed, a practice already used by many electrical and mechanical contractors.
■ Its Effect: This added language provides an additional level of protection for the public and the electrical professional concerning disconnects that have no internal covers that protect live parts. Exposure of these live parts to unqualified individuals could cause injury or death.
Revision – 440.14
Location
■ What Changed: A reference to 110.26(A) was added in Section 440.14, which now makes it clear that working space clearances are required for air-conditioning and refrigerating equipment. Many HVAC contractors install their equipment per the manufacturer’s specifications but pay little attention to the minimum required clearances in NEC 110.26 for disconnects that require servicing.
■ Its Effect: This added information makes it clear to the inspector and installer that minimum clearances must be maintained at air-conditioning and refrigerating disconnects.
Revision – 445.18(A) & 445.19
Disconnecting Means & Emergency Shutdown of Prime Mover
■ What Changed: New language was added to (A), permitting the disconnecting means to be located within the generator behind a hinged cover, door, or enclosure panel. When the generator disconnecting means is located in the generator, a field-applied label has to be provided indicating
the location of the disconnecting means. Additional modifications are made for 445.18(A) to clarify the permitted locations for emergency disconnecting means and marking means. Field labeling requirements have been added, providing clarity for the purpose of the disconnecting means to aid first responders.
A new Section 445.19 will separate the generator emergency shutdown requirements from the generator disconnect requirements. Generators with greater than 15 kW rating located at other than one- and two-family dwelling units are to be equipped with a remote emergency stop switch that will shut down the prime mover. This switch is to be located outside the equipment room or generator enclosure at a readily accessible location and meets the requirements found at 445.19(A)(1) and (A)(2).
New language at (C) clarifies that the emergency shutdown device located at one- and two-family dwelling units mounted on the exterior of the generator enclosure meets the requirements of this section. This device is to be marked as the “Generator Emergency Shutdown” and meets the requirements of 110.21(B).
■ Its Effect: There has been confusion among electrical professionals as to the requirements for generator disconnecting means and the requirements for emergency shutdown of the prime mover. These revisions help to clarify the requirements and aid in the usability of the Code. This work will help the installer and AHJ better understand these requirements.
New – 450.2
Interconnection of Transformers
■ What Changed: New guidance was added for transformer interconnection and operation requirements within Article 450. This change addresses how the provisions in the article are to be applied to transformers either individually or interconnected as a single unit.
■ Its Effect: There should not be much of an effect on the electrical professional regarding this change. Much of this addressed NEC Style Manual concerns and correcting some issues that occurred in the 1987 code cycle.
New – 470.2
Reconditioned Equipment
■ What Changed: Section 470.2 is now the new placeholder for reconditioned equipment, indicating that reconditioning of a resistor is not permitted and that reactors shall follow manufacturers’ guidelines. Resistor manufacturers have made it clear that resistors are not to be reconditioned. Reactor manufacturers provide guidelines on the reconditioning of these apparatus in their installation instructions and also have standards for the reconditioning of them.
■ Its Effect: This change will provide clear information to all electrical professionals regarding the reconditioning allowances for resistors and reactors.
New / Relocation – Article 495
Equipment Over 1000 Volts AC, 1500 Volts DC, Nominal
■ What Changed: All the requirements previously found in Article 490, Equipment Over 1000 Volts, Nominal, have been moved to Article 495. This will provide an article that will contain all installation requirements pertaining to equipment over 1000 volts AC and 1500 volts DC in future NEC additions.
■ Its Effect: This will result in easier use of the Code when searching for requirements on this topic.